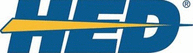

Catalog excerpts
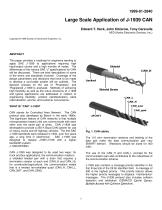
Large Scale Application of J-1939 CAN Edward T. Heck, John Kitzerow, Tony Caravella HED (Hydro Electronic Devices, Inc.) Copyright © 1999 Society of Automotive Engineers, Inc. ABSTRACT This paper provides a roadmap for engineers wanting to apply SAE J-1939 to applications requiring high input/output counts and a high number of nodes. The differences of the various SAE “J” specifications for CAN will be discussed. There are brief descriptions of some of the terms and standards involved. Coverage of the design parameters and decisions that have to be made to develop a survivable system will be outlined. The decision process on the use of “Proprietary” and “Registered J-1939 is analyzed. Methods of achieving high flexibility as well as the future directions of J-1939 and typical applications are addressed in relation to engineering flexibility, product standardization, parts rationalization, service, and customer convenience. WHAT IS “CAN” J-1939? CAN stands for Controlled Area Network. The CAN protocol was developed by Bosch in the early 1980s. The significant feature of CAN networks is that multiple microprocessor based units can communicate with each other over the same pair of wires. CAN J-1939 was developed to provide a 250 K Baud CAN system for use on heavy trucks and off-highway vehicles. The first SAE J-1939 standards were released in 1994- over five years ago, a long time in electronics! SAE J-1939 was designed to replace J1587/J1708 with a higher bandwidth system. J-1939 DESIGN \ Fig. 1, CAN cables. The 110 ohm termination resistors and twisting of the data pair make the data communication pair very EMI/RFI tolerant. (Resistors should be sized for 400 mW) CAN J-1939 was designed to be used two ways: for truck and bus applications, the communication media is a shielded twisted pair with a drain that requires a termination resistor at each end (CAN_H and CAN_H); for construction/agricultural, the communication media that is a twisted non-shielded quad (CAN_H, CAN_L, CAN_BAT, and CAN_GND). The use of the CAN_H and CAN_L concept for the communication pair also contributes to the robustness of the communication scheme. J-1939 also contains a message priority identifier in the first three bits of the 29 bit identifier field. A message of 000 is the highest priority. This priority feature allows the higher priority messages to displace “maintenance” messages. The J1939 protocol also includes collision detection and arbitration (CSMA/CD Carrier Sense, Multiple Access with Collisio
Open the catalog to page 1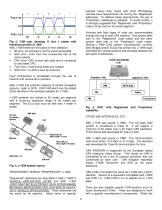
purpose heavy duty trucks and most Off-Highway vehicles have requirements not met by the “Registered” addresses. To address these requirements, the use of “Proprietary” addresses is adopted. To avoid conflict, it is strongly suggested that “Registered” and “Proprietary” codes not be used on the same segment. Vehicles with both types of code can accommodated through the use of dual CAN systems. One system talks only to the “Registered” code nodes and the other system talks only to the “Proprietary” code nodes. Several J-1939 CAN system manufacturers currently offer Bridges and/or ECUs that...
Open the catalog to page 2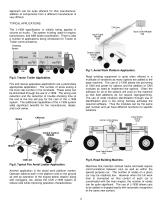
approach can be quite efficient for that manufacturer, addition of components from a different manufacturer is very difficult. TYPICAL APPLICATIONS The J-1939 specification is initially being applied in volume on trucks. The system is being used for engine, transmission, and ABS brake coordination. There is also a number of applications being introduced for Tractor to Trailer communications. Fig 7, Aerial Work Platform Application. Road building equipment is quite often offered in a multitude of variations as many options are added to the base machine. The use of J-1939 allows the...
Open the catalog to page 3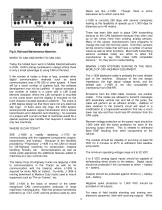
Deere are like J-1939. Though, there is some discussion as to which came first. J-1939 is currently 250 kbps with several companies looking at the feasibility of speeds up to 1,000 kbps for distances up to 40 meters. There has been little work to place CAN transmitting sensors on the CAN backbone because they often cost up to ten times more than existing analog sensors. Many of the sensor manufacturers have programs to change this over the next few years. Until then, sensors will be wired to nodes that will have a number of sensor inputs as well as other functions. Most CAN transmitting...
Open the catalog to page 4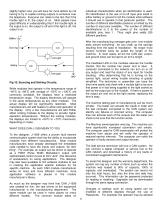
individual characteristics when pin identification is used. Pin identification is the use of on-off input pins wired to either battery or ground to tell the module what software it should use to operate in that particular position. The number of different identifiable positions is limited by the number of input pins available. The number of different identifications is 2 to the power of the number of available pins, less 1. Thus, eight pins yields 255 different positions. slightly higher cost, you will save far more dollars by not having to try to explain sinking outputs to someone over the...
Open the catalog to page 5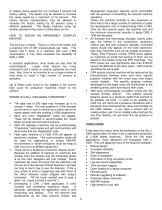
to reduce swing speed but not increase it beyond the factory setting. The dealer may be allowed to increase the swing speed by a maximum of 10 percent. The factory service representative may be allowed to increase the factory setting by 20 percent using a different password. The design engineer using yet another password may have no limits place on him. HOW TO DESIGN AN IMPROBABLY COMPLEX MACHINE The formula is simple. There is a limit of 30 nodes with a practical limit of 255 inputs/outputs per node. This means that if there is a machine with over 7,650 input/outputs, it may have exceeded...
Open the catalog to page 6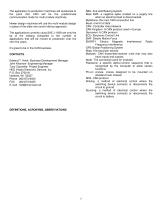
ABS- Anti-skid Braking System Back EMF- a negative spike created on a supply line when an electrical load is disconnected. Backbone- the main CAN connection line Baud- one bit of data CAN- Controller Area Network CAN Kingdom- A CAN protocol used in Europe Devicenet- A CAN protocol ECU- Electronic Control Unit EMF- Electro Motive Force EMI/RFI- Electro Magnetic Interference/ Radio Frequency Interference GPS-Global Positioning System Kbps- Kilo baud per second Modules- CAN transmitter/receiver units that may also have inputs and outputs Node- The connection point for modules Password- a...
Open the catalog to page 7All HED Inc. catalogs and technical brochures
-
HED Application
12 Pages
-
Basic Electronics
32 Pages
-
CAN and Multiplexing
30 Pages