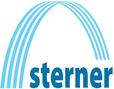
Catalog excerpts
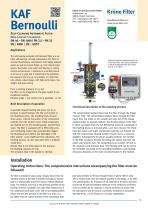
filter@krone-filter.com www.krone-filter.com Self-Cleaning Automatic Filter Non-Contact Cleaning DN 40 – DN 1000 | PN 2,5 – PN 25 EN / ANSI / JIS / GOST Applications The self-cleaning automatic KAF Bernoulli filter is a versatile self-cleaning, virtually maintenance-free filter for removal of particulate contaminants from highly polluted waters as well as process fluids e.g. from natural water sources (sea water, river water) and heating or cooling circuits and processes. It operates at a working pressure as low as 0.3 bar and is characterized by extremely low pressure loss of 0.09, for example, at a high flow rate, simple, robust design, with high performance, low weight, and space saving. Electronic standard multifunctional unit of the KAF filter. Alternatively Siemens or Allen Bradley/Rockwell for controlling up to 10 filters. Flush outlet • from a working pressure of 0.3 bar • the filter can be integrated in the pipe system in any installation position • filtration stage ≥ 160 microns (100 μ possible) - 10 mm Inlet Brief description of operation Functional description of the cleaning process A specially shaped flushing disk gives rise to an increase in speed between the disk and strainer in the flushing process. The resulting local pressure drop causes internal evacuation of the contaminant particles from the strainer insert. Solid components are flushed out via the simultaneously opened flush valve. The filter is equipped with a differential pressure monitoring system that automatically triggers the flushing process before any blockages in the filter strainer cause significant flow reductions. The flushing process can also take place after a predetermined time. • Filtrate flow is not interrupted in this process; the flushing volumes are low. • The pressure drop in the system is minimal. The contaminated medium flows into the filter through the flange marked inlet. The contaminated medium flows through the filter insert from the inside to the outside and exits out of the flange marked outlet as cleaned medium. The flushing phase of the filter is either activated when the set differential pressure is attained, or the flushing phase is activated after a set time interval. The flushing valve opens and larger contaminant particles are flushed out with the continuously flowing medium stream due to a pressure gradient. Subsequently the piston usually performs two strokes in the filter strainers, thereby increasing the speed between the piston and strainer wall. The contaminants are sucked off due to the resultant local pressure drop. The flushing time can be set by the controller according to the operating conditions, and flushing frequency depends on the level of contamination in the medium. Installation Operating instructions: The comprehensive instructions accompanying the filter must be followed! The filter is installed in pipes using flanges. Ensure that the standard version of the filter is installed vertically or horizontally in a mechanically stress-free manner without additional loads. The medium must flow in the direction specified on the housing. Incorrect installation can cause filter malfunctions. If the contaminant drain pipe is laid with an ascending gradient ensure that the inlet pressure of the filter is at least a 0.3 bar higher than the counter pressure in the contaminant drain pipe (pay attention to the loss through friction in pipes). Before using with a medium other than the medium specified in the design, or for different operating data, the resistance of the materials of the parts and seals touched by the pressure-bearing membrane to the medium to be filtered must be checked by the customer; it may be necessary to consult with the manufacturer and to execute a conformity evaluation in accordance with PED EN 97 / 23 EC (if there is a CE-mark requirement). 01 04/2014 © by Krone Filter Solutions GmbH, su
Open the catalog to page 1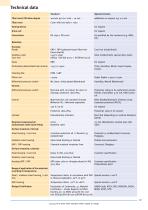
Filter insert/filtration degree Filter cover Venting device Drain unit Connections Materials: Housing: Plastic Stainless steel Cast Iron Seals Perforated plate/slotted hole strainer Flushing disk Piston rod Differential pressure switch Version: Differential pressure switch Control Cylinder Required compressed air Contaminant outlet valve fitting Surface treatment, internal: Steel housing / Cast Iron Stainless steel housing GRP / FRP housing Surface treatment, external: Steel housing / Cast Iron Stainless steel housing Housing GRP / FRP Range of application of the materials according to...
Open the catalog to page 2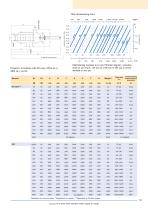
*Dependent on pressure phase, **Rubberlined on request, ***Dependent on filtration degree 04/2014 © by Krone Filter Solutions GmbH, subject to chan
Open the catalog to page 3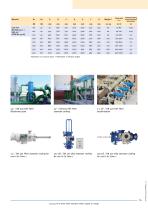
24" / DN 600 KAF Filter Bioethanol plant 24" / DN 600 KAF Filter seawater cooling 14" / DN 350 Filter seawater cooling for use in Ex Zone 1 200 JIS / DN 200 ship seawater cooling for use in Ex Zone 1 300 JIS / DN 300 ship seawater cooling for use in Ex Zone 1 04/2014 © by Krone Filter Solutions GmbH, subject to change 04
Open the catalog to page 4All Sterner AS catalogs and technical brochures
-
OxyGuard Handy Salinity
2 Pages
-
OxyGuard Handy Atmosphère
2 Pages
-
OxyGuard Polaris 2 TGP
2 Pages
-
OxyGuard Polaris 2 TGP
2 Pages
-
OxyGuard CO2 Portable
2 Pages
-
NESTE GENERASJON CO2-LUFTER
2 Pages
-
NP Innovation
3 Pages
-
KAF Bernoulli Filter
8 Pages
-
KSF
7 Pages
-
SMOevo Ozone Systems
4 Pages
-
SMOevo Ozone Systems
8 Pages
-
WEDECO GSO Series
2 Pages
-
Spektron UV Series
8 Pages
-
Quadron UV series
8 Pages
-
Duron UV System
8 Pages
-
AquaZone
8 Pages
-
Complete systems Aquaculture
5 Pages