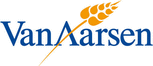
Catalog excerpts
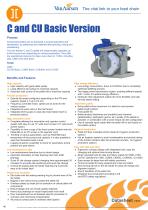
C and CU Basic Version Process Animal feed pellets can be produced in several diameters and hardnesses, by pelletizing raw materials after grinding, mixing and conditioning. The Van Aarsen C and CU pellet mill range enable capacities up to 60 tons per hour depending on various parameters. They offer low operational costs per ton feed, even down to 1 €/ton, including dies, rollers and wear parts. Range C600 CU750 Basic, CU900 Basic, CU900XL and CU1200 Benefits and Features High capacity ▶ High capacity with good pellet quality ▶ Large effective die surface to maximize capacity ▶ Automatic load control of the pellet mill to maximize capacity Flexible production ▶ Optimal die speed configured, depending on the PDI and capacity. Speed 4.7 up to 9.4 m/s ▶ Frequency controlled motor, speed can be tuned for the various recipes ▶ Integrated by-pass valve in the inlet funnel ▶ Integrated 2nd by-pass in case also heat treated mash is produced (option) High energy efficiency ▶ Low energy consumption, down to 8 kWh/ton due to completely optimised pelleting process ▶ Two-stage power transmission system, enabling different speeds with 1 motor, for optimal energy efficiency ▶ Hydraulic roller adjustment (option) for more flexibility and safe formula based setting High feed quality ▶ Extra pellet knives (maximum 4 in total) for more precise pellet length (option) ▶ Food grade fat ▶ Better physical (hardness and durability) and chemical (gelatinisation, pathogenic germs, etc.) quality of the pellets is High automation level possible, in combination with a tuned recipe and die configuration ▶ Complete pelleting line automation and operator control ▶ Use of cascade liquid coater after the pellet mill to add liquids on system with easy to use 12” wide touch screen (19” wide touch hot pellets (option) screen option) ▶ Possibility to view a copy of the touch screen located near the Hygienic production ▶ Pellet mill door insulated and/or heated for hygienic production Pellet Mill on an PC screen in the operator room (option) ▶ Trending of various parameters, such as Pellet Mill load, ▶ Hot air hygienic system to avoid condensation and provide drying temperature of the product and capacity. It is also possible to of the product remains after the production process, for hygienic view this information back in time production (option) ▶ Logging of alarms; possibility to check for parameters during present and past alarms Easy and safe operation ▶ Ergonomic compact design with integrated hoist, easy die Low maintenance costs changing and optional slow turning device ▶ Low maintenance downtime due to robust design ▶ Motor operated hoist for dies and rollers (option for C600, C750, ▶ Automatic lubrication of roller bearings and main shaft CU750, standard for C900, CU900, C900XL, CU900XL, CU1200) bearings ▶ Quick fit® die change system (changing time approximately 30 ▶ Easy access by large door with safety provisions ▶ Tool set included for easy replacement of die and rollers minutes) for accurate die positioning and quick die change ▶ Slow turning device on the die holder for easy die change and ▶ Conical die seating with die holder wearing ring to prevent alignment (option) wear of die holder itself ▶ Sound insulation of the pellet mill Design and durability ▶ Designed and constructed according to CE ▶ Die holder with die seating wearing ring to prevent wear of the and ATEX safety regulations die holder ▶ Magnet in the inlet funnel to protect the pellet mill ▶ Overload safety by break pin for protection of critical pellet mill components ▶ Robust design and use of high quality materials ▶ Heavy duty bearings on robust forged steel main shaft ▶ Door manufactured out of stainless steel for prevention of corrosion and minimizing contamination ▶ All product contact parts in stainless steel (option) No rights can be claimed, based on the information in this document. Descriptions and illustrations are sub
Open the catalog to page 1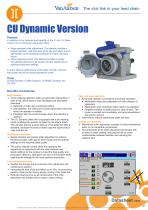
CU Dynamic Version Process In addition to the features and benefits of the C and CU Basic version, the CU Dynamic range also offers: ▶ Motor-operated roller adjustment. This feature provides a simple operation, with less wear of the die and rollers and an optimization of the operating conditions for each individual recipe. ▶ Active rollerslip control. This feature provides a trouble free pelleting process of all recipes and the opportunity to optimize production settings. In short: optimal performance of the pellet mill with minimum man power and at the lowest operational costs! Range CU750...
Open the catalog to page 2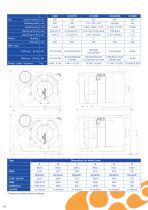
Diameter mm Main motor Weight (static / dynamic) * Dimensions for Basic version on request
Open the catalog to page 3All Van Aarsen International B.V. catalogs and technical brochures
-
Ingredient Dosing Units
4 Pages
-
GD Hammer Mill
4 Pages
-
Steam mixer
2 Pages
-
Crumbler
2 Pages
-
2D Hammer Mill
2 Pages
-
MultiPreMix paddle mixer
2 Pages
-
Cooling - Counterflow Cooler
2 Pages
-
LTV Dosing Screws
2 Pages
-
Transport - Piping
6 Pages
-
Feed Mill Automation
4 Pages
-
Hygiene - Hot Air Systems
2 Pages
-
Transport - Bucket Elevator
2 Pages
-
Mixing - Vertical Mixer
1 Pages