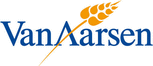
Catalog excerpts
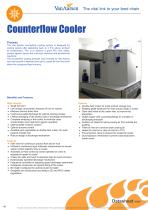
Counterflow Cooler Process The Van Aarsen counterflow cooling system is designed for cooling pellets after pelletizing back to ± 5°C above ambient air temperature. This is to achieve a good PDI, flow ability, protect against decay and minimize chemical and biochemical reactions. The counterflow cooling principle was invented by Van Aarsen and has become a standard blue print, copied all over the world within the compound feed industry. Benefits and Features High capacity ▶ Small foot print ▶ Low energy consumption because of low air volume ▶ Minimum service down time ▶ Continuous pellet discharge for optimal cooling process ▶ Limited damaging of the product due to discharge mechanism ▶ Complete emptying of the cooler, to minimize cross contamination and maximize hygienic operation ▶ Optimal pellet moisture content ▶ Optimal process control ▶ Available and upgradable as double deck cooler, for quick product change-over ▶ Robust design of discharge mechanism Features ▶ Inlet valve for continuous product flow and air lock ▶ Ultrasonic continuous layer thickness measurement to ensure and/or control retention time in cooler ▶ Automatic air flow control by motor-operated air valve to regulate air speed in cooler ▶ Cooler bin walls and hood in stainless steel to avoid corrosion ▶ Hydraulically operated discharge mechanism ▶ Frequency controller for adjusting speed discharge mechanism ▶ Octagonal construction for optimal filling of the cooler ▶ Bin height configured for optimal (build in) height ▶ Designed and constructed according to CE and ATEX safety regulations. Options ▶ Double deck cooler for quick product change-over ▶ Rotating pellet distributor for even product layer in cooler ▶ Clam shell valve at the cooler inlet, to improve fat absorption ▶ Outlet hopper with connecting flange on crumbler or discharging transport ▶ Outdoor air intake for taking cooling air from outside the building ▶ Filter for inlet air to ensure clean cooling air ▶ Heater for inlet air in case of cold air (<5°C) ▶ Fire protection valve to prevent fire inside the cooler ▶ Dust explosion membrane to prevent dust explosions inside cooler No rights can be claimed, based on the information in this document. Descriptions and illustrations are subject to change, due to c
Open the catalog to page 1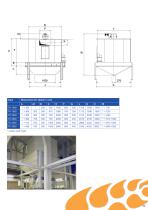
* variable shaft height
Open the catalog to page 2All Van Aarsen International B.V. catalogs and technical brochures
-
Ingredient Dosing Units
4 Pages
-
GD Hammer Mill
4 Pages
-
Steam mixer
2 Pages
-
C and CU Basic Version
3 Pages
-
Crumbler
2 Pages
-
2D Hammer Mill
2 Pages
-
MultiPreMix paddle mixer
2 Pages
-
LTV Dosing Screws
2 Pages
-
Transport - Piping
6 Pages
-
Feed Mill Automation
4 Pages
-
Hygiene - Hot Air Systems
2 Pages
-
Transport - Bucket Elevator
2 Pages
-
Mixing - Vertical Mixer
1 Pages