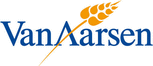
Catalog excerpts
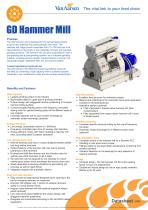
GD Hammer Mill Process The GD hammer mill is designed for the animal feed industry, to grind raw materials into small particles and meal. The hammer mill range covers capacities from 10–100 tons per hour, dependening on the types of raw materials, formula and required grinding structure. The hammer mill can be incorporated in both a pre-grinding and a post-grinding system, as a complete grinding solution; including pre-bin, feeder, magnet cleaner, hammer mill, discharge hopper, aspiration filter, fan and control system. Lowest operational costs per ton The GD hammer mill offers the lowest operational costs per ton feed by combining a high capacity with a customer specific production, low maintenance costs and low energy consumption. Benefits and Features High Capacity ▶ Largest grinding surface in the industry ▶ Big breaker plates in upper part of grinding chamber ▶ Unique design with staggered hammer positioning to increase hammer hitting surface ▶ Compact shaped feeding device with frequency controlled dosing roller for optimal feeding speed of the different types of raw material. ▶ Increased capacity due to quick screen exchange by automatic screen exchange (optional) Energy efficiency ▶ Low energy consumption (down to 7 kWh/ton) ▶ Frequency controlled main drive for energy cost reduction ▶ Energy efficient motors with direct coupling to hammer mill rotor, according latest European standards Low maintenance costs ▶ Minimal wearing costs due to unique designed breaker plates and long lasting hammers ▶ Perfect balance of the hammer mill rotor due to precise tolerances of the hammers ▶ Bi-directional inlet flow director and two-direction rotor for optimal use of the hammers on all 4 sides ▶ the hammers can be replaced by one operator in a short maintenance action which decreases the service down time ▶ Shock absorbers minimizing vibrations to the building (on concrete as well on steel floors) ▶ Integrated magnet with automatic cleaner Easy and safe operation ▶ Easy access by large special designed doors opening to the top for changing hammers or inspection ▶ Hammer mill enables only 1 person to replace hammers safely in a short period of time ▶ Hopper under hammer mill with optional explosion relieve panel (optional) ▶ Low noise level (about 94dB) by the unique design with staggered hammer positioning ▶ Designed and constructed according to CE and ATEX safety regulations High feed quality ▶ Excellent feed structure for individual recipes ▶ Magnet and collecting bin for automatic Ferro parts separation included in the feeding device ▶ Aspiration system (optional) ● Filter integrated in hopper below hammer mill (less contamination) ● Filter separated from hopper below hammer mill in case of limited space Flexible production ▶ Customer specific structure milling by the use of frequency converter ▶ Automatic screen exchange for 3 different screen sizes (optional) High automation level ▶ Complete control of the hammer mill by a Siemens PLC including a multi panel touch screen ▶ Highest safety by amongst others temperature monitoring and overflow sensors ▶ Vibration detection on the bearings for early detection of wearing (optional) Design ▶ Compact design. The GD hammer mill fits in the existing space in case of a replacement ▶ Durable and robust design by use of high quality materials, lifetime up to 30 years No rights can be claimed, based on the information in this document. Descriptons and illustrations are subject to change, due to co
Open the catalog to page 1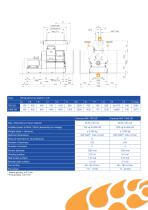
Hammer Mill 700 GD Max. dimensions of input material Screen diameter Grinding surface Nett screen surface Breaker plate surface Installed power at 50Hz / 60Hz (depending on voltage) Weight (static = dynamic) Hammer dimensions Rows of hammers on circumference Number of hammers Number of screens * Normal grinding, ≥ Ø 2 mm ** Fine grinding,
Open the catalog to page 2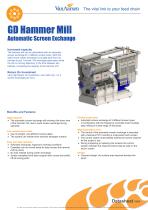
Automatic Screen Exchange Increased capacity The hammer mill can be refurbished with an automatic screen exchange for 3 different screen sizes. With this option each screen exchange is brought back from 20 minutes to just 1 minute. The exchange takes place while the mill is running stationary in the time between two batches, increasing the capacity of the hammer mill. Very high Return On Investment, even with only 1 or 2 screen exchanges per hour. Benefits and Features High Capacity ▶ The automatic screen exchange will minimize the down time of the hammer mill, due to quick screen exchange...
Open the catalog to page 3All Van Aarsen International B.V. catalogs and technical brochures
-
Ingredient Dosing Units
4 Pages
-
Steam mixer
2 Pages
-
C and CU Basic Version
3 Pages
-
Crumbler
2 Pages
-
2D Hammer Mill
2 Pages
-
MultiPreMix paddle mixer
2 Pages
-
Cooling - Counterflow Cooler
2 Pages
-
LTV Dosing Screws
2 Pages
-
Transport - Piping
6 Pages
-
Feed Mill Automation
4 Pages
-
Hygiene - Hot Air Systems
2 Pages
-
Transport - Bucket Elevator
2 Pages
-
Mixing - Vertical Mixer
1 Pages