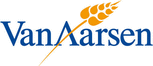
Catalog excerpts
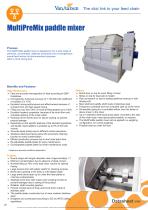
MultiPreMix paddle mixer Process The MultiPreMix paddle mixer is designed to mix a wide range of premixes, concentrates, additives and liquids into a homogeneous animal feed mixture for pharmaceutical purposes, within a short mixing time. Benefits and Features High effectiveness ▶ Fast and accurate homogeneity for feed according to GMP+ Guidelines. ▶ Homogeneity: Achieved accuracy of 1:100.000 with coefficient of variation CV <5%* ▶ Excellent mixing performance and effectiveness because of compact form and high speed mixing ▶ Filling can vary from 30% of nominal filling degree up to 100% ▶ Excellent hygienic properties, because of its round form and complete opening of the mixer outlet ▶ Hydraulic driven bomb door for secure closing, to prevent product leakage ▶ Depending on the specific features of the blended ingredients and liquids, liquid addition is possible up to 6% of the total volume ▶ Accurate liquid dosing due to different nozzle executions ▶ Stainless steel liquid spray pipes with pneumatic cleaning function to avoid contamination ▶ Efficient production process due to short total batch time ▶ Re-adjustable paddle plates for easy maintenance ▶ Exchangeable paddle plates for lower maintenance costs Options ▶ Bomb-door on top for quick filling of mixer ▶ Slides on top for less build in height ▶ Pipe connection on top for adding additives (manual or with dosing unit) ▶ Main shaft and paddle shaft made of stainless steel ▶ Frequency controlled drive for controlled start-up of the mixer ▶ De-aeration piping for a controlled airflow, from bin below or above mixer, to the mixer ▶ Up to 3 stainless steel liquid spray pipes, mounted to the side of the mixer body; more spray pipes possible, on request ▶ The MultiPreMix paddle mixer can be applied in a weighing configuration, for control-weighing ▶ Possible start-up under full load * recipe and process conditions dependent Features ▶ Round shape with length–diameter ratio of approximately 1:1 ▶ Minimum contamination due to absence of dead corners ▶ Nominal filling at 70% of the total mixer volume for optimal mixing ▶ Large access door with safety switch for cleaning purpose ▶ Bomb-door opening in the body is a 90 degree angle ▶ Large bomb doors open up to under the head plates to minimize contamination ▶ Sealings bomb door with scissor and scraping function to prevent leakages due to caking of the product ▶ Reliable, shaft mounted gearbox ▶ Product contact parts of body and bomb doors made of stainless steel ▶ The paddle plates constructed out of wear resistant stainless steel ▶ Designed and constructed according to CE and ATEX safety regulations 20 No rights can be claimed, based on the information in this document. Descriptions and illustrations are subject to change, d
Open the catalog to page 1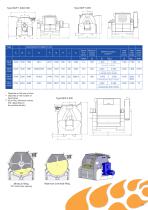
Bomb door above Minimum product content Maximum product content*** Total mixer volume Total mixer weight Motor power mixer * Depends on the type of drive ** Depends on the number of liquid pipes *** Kg or liter, whichever comes first, depending on the product density! Minimum filling *90° bomb door opening
Open the catalog to page 2All Van Aarsen International B.V. catalogs and technical brochures
-
Ingredient Dosing Units
4 Pages
-
GD Hammer Mill
4 Pages
-
Steam mixer
2 Pages
-
C and CU Basic Version
3 Pages
-
Crumbler
2 Pages
-
2D Hammer Mill
2 Pages
-
Cooling - Counterflow Cooler
2 Pages
-
LTV Dosing Screws
2 Pages
-
Transport - Piping
6 Pages
-
Feed Mill Automation
4 Pages
-
Hygiene - Hot Air Systems
2 Pages
-
Transport - Bucket Elevator
2 Pages
-
Mixing - Vertical Mixer
1 Pages